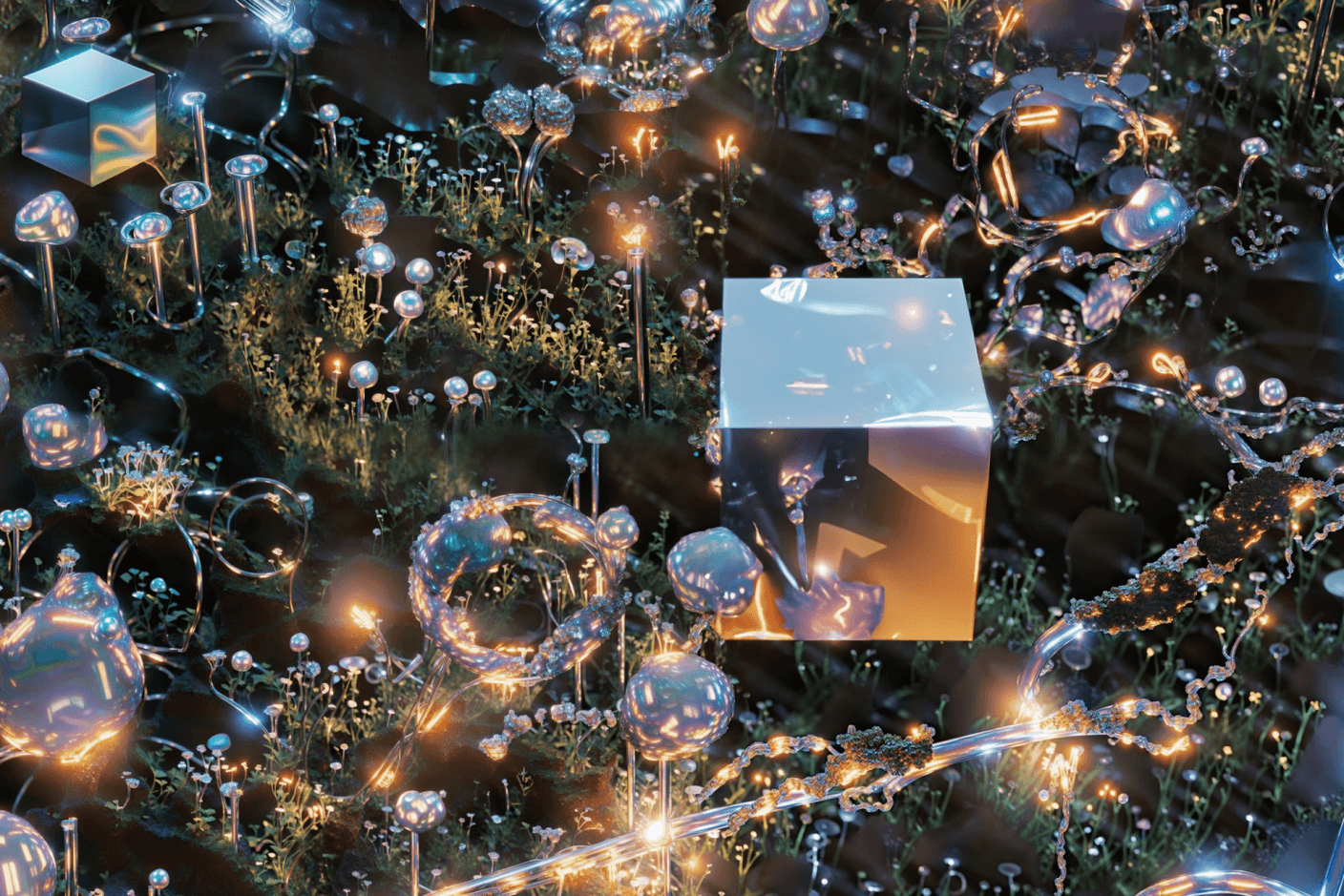
Industrial Biome
How can factories behave like forests?
While technology continues to advance, it continues to serve outdated, socially and environmentally untenable industrial models. It’s time for us to heal the means — and the ends — of industry.
Imagine a forest. You think of trees. Imposing, dense, green. Or maybe of the unmistakable fragrance of pine needles or of enveloping silence. A natural, self-sustaining space.
Now imagine a typical factory. A sprawling silo-scape, a mass of metal, gnashing machinery, belching smoke. It’s easy to place them as opposites. One regenerative, one extractive. One positive, one negative. But both are highly complex, efficient ecosystems that have evolved to produce, transform and distribute resources. And both serve humans, albeit to varying ends.
How much of what sets them apart could be mitigated by implementing new operating models?
In our work with industry leaders over the last 16 years, we have been pulled towards a growing meshwork of concepts designed to help any manufacturer achieve greater balance between thriving industry and thriving nature. An adaptive and modular model that aims to shift our methods of make and consumption; we call it the Industrial Biome.
A new industrial paradigm
One can break down a factory’s operation in terms of inputs, outputs and enablers. Energy becomes action, material becomes product and every process is connected and enabled by an elaborate system of humans and technologies working together. But, whereas a forest system ultimately yields nutrient, industrial systems’ inputs, outputs and enablers create waste and pollution — at scale.
So let us imagine a different type of factory.
A lean, looped system that metabolizes its own waste and uses its byproducts as feedstock. Reconfigurable and responsive, this thriving factory is largely self-regulating. Sensor technology connected to a central digital nervous system allows it to read and automatically adjust the flow of resources according to different environmental conditions and phases of demand.
This flexibility extends to production where versatile, adaptive robotics are programmed to fulfil multiple tasks depending on current product lines and market needs.
Resourceful methods of make, such as additive manufacturing processes and on-demand manufacturing infrastructure help the factory to only produce what it needs and knows it can sell, reducing both waste and valuable storage footprint. Rather than a monolithic giga-factory, the factory is one small production and innovation node within a network, fed by regional raw material hubs that follow natural cycles.
The thriving factory considers the long-term purpose of its products, and provides the framework for services beyond their manufacture and distribution. Conscious of its responsibility within the broader industrial ecosystem, disassembly and product end-of-life have become as important as assembly in its design-to-make pipelines. The prioritized use of mono-materials and mechanical fasteners make some product parts easier to dismantle and recycle, while biomaterials help others degrade organically.
Innovation in the thriving factory is invigorated by collaboration across industries and shared knowledge systems that invite more — and more imaginative — solutions to materials, technology and processes. Programs to retrieve and recycle used materials and broken goods drive new research and development streams around conscious production, and increase their economic and logistical viability.
Throughout the thriving factory, integral physical components and data are standardized so that they can be transferred between different products and processes and reduce obsolescence. This, in combination with information hubs and accessible learning resources, empowers consumers to fix, upgrade and keep their products longer — whether they be smart devices, bicycles or apparel.
As an arterial part of its local natural and socio-economic landscape, the thriving factory is committed to being a good and conscientious neighbor. It both draws from and enriches the local community.
The entire organism is designed to conserve nutrients within and beyond its premises and replenish what it extracts. Rain and waste water is collected and treated for reuse, while smart grids power the factory with renewable energy. Any surplus is fed back into the grid to augment local supply with green energy while excess materials are sorted and sold.
The thriving factory thrives because it operates both with and within a healthy industrial biome. Not apart from nature but, like us — and because of us — a part of it.
An inclusive and nurturing working environment, the thriving factory maintains healthy conditions over all dimensions of its form and function. It is constructed to catch and optimize natural light, facilitate barrier-free movement, insulate against disruptive noises and smells, and integrate green spaces inside and around its premises that improve air quality as much as they provide points of beauty. More holistic success metrics mean work is organized as much around productivity as around providing opportunity for employee development and creative actualization.
It is an experimental space that constantly explores new technology, but implements it sensitively in places that relieve repetitive or physically arduous tasks, with intuitive interfaces that empower more frictionless human-machine collaboration. Regenerative and resilient — the thriving factory thrives because it operates both with and within a healthy industrial biome. Not apart from nature but, like us — and because of us — a part of it.
Stewarding Change
We know industry in and of itself is not bad.
A dynamic monument to human ingenuity, by facilitating the creation of goods and services, it has allowed most of us to enjoy a far greater level of comfort on planet earth than our more lo-fi ancestors. It is also the engine that will ultimately drive any meaningful shift to regenerative technologies and materials.
What is bad is the material and scale of typical industries’ disruption to our environment. And this is something well within our power to change.
Our vision of a thriving factory is not far-fetched. There are brands and manufacturers that have already integrated several of the concepts described and, what’s more: to great effect.
But to achieve a thriving ecosystem takes clear intention over two speeds — a willingness to commit to the slow and steady work, and the courage to take the bold, immediate decisions. This is why we designed the Industrial Biome model to follow the unique contours of each client’s needs and opportunities and identifies which interventions — be they a revised vision, refined tools or processes — can be applied at which time. In 2023 we defined our research and development themes to reinforce each pillar of this growing work (see below).
The most important thing we have learned, is that change doesn’t have to be absolute to be effective. Big, long-term change happens in tandem with small, short-term changes; and industrial ecosystems, in all their complexity, offer not one but a plethora of opportunities to manifest change. The question is, where do you want to start?
Find out more
To find out more about our Industrial Biome model, or to understand where your business can optimize its operations for a thriving future, get in touch with Adrien Hobt.
Visuals created by Misha Gurovich for PCH Innovations.
Words + diagrams by Gabriella Seemann, Creative Director at PCH Innovations.